石油化工生产工艺中,高温、低温操作工况很多,存在高温、低温设备和管道不采取隔热保温工艺或隔热保温不合理的现象。在生产过程中,设备和管道会不断向外界释放或吸收大量的热量而造成大量的热损,其至有时都不能保证正常的生产工艺条件,所以在石油化工生产中,对高温、低温设备和管道采取隔热保温工艺是有效防F止热损、保证正常生产工况的有效手段。隔热工程分为保温和保冷,本篇论文内容只涉及保温工程方面。石油化工生产对工艺条件要求非常苛刻,生产装置中的设备、管道保温效果直接决定着设备、管道内工艺介质能否正常平稳运行,甚至直接影响石化产品的质量水平。再者保温层是设备、管道的“外衣”,直接影响着生产装置的美观。基于以上原因,设备、管道的保温若想既要节能降耗、还要美观,就要不断地对各类保温材料及其制品进行性能改进提升,不断地研发性能更优的保温材料来满足需求,还要对保温的施工方法进行改进,保温施工过程质量控制进行强化,同时还要加强设备、管道在装置运营过程中的科学管理、统筹考虑。保温工程一方面要充分考虑生产工艺条件大力推广高效节能的保温设计结构,选择质优价良的保温材料及其制品;另一方面要在保温施工的过程中严格按照施工的标准进行施工,并严格保证施工的质量验收;在装置运营过程中加强数据检测,及时维修维护,确保热量损失指标达标。高效的保温结构不JJ能够有效防F止设备、管道等运营过程中的热量损失、保证满足生产工艺条件,而且也使装置运营操作人员的劳动环境得到改善,有一个良好的A全操作环境,F止烫S等事故发生。长距离输送高温介质管道的热量损失需严格控制,避免管道起止温差超标,确保满足生产工艺所需要的温度参数。在冬季,保温可F止设备、管道内液体介质的冻结而破坏设备、管道:当设备、管道内的介质操作温度低于环境空气露点温度时,采用保温隔热可有效F止在设备、管道的表面出现结露现象:保温还可减少各类工艺设施、炉类设备及热力热网等的热量损失,达到节约能源,增加使用周期,提高产能的目的[48,491。在石化装置之间和装置内部都铺设有大量的管道,而管道的散热损失在装置能耗中占据较大的比例。2015年中G石化曾对炼化企业管道进行了系统的调研测试,该项防腐保温调研测试共选取不同介质温度、不同管径的各类样本工艺管线216根,按照中G石化现行标准《石油化工设备和管道隔热工程设计规范》SH/T3010-2013中规定的最D允许热损失量进行测评,大于最D允许热损失量标准的(超标)为 85 根,占总样本数的39.8%,即炼化企业管道中约有近四成管道散热损失量不达标,其中散热损失量超标程度达到标准规定50% 以上的管道数量占总超标管道数的47.1%。管道热损失量超标率随介质温度的升高而增D,中压蒸汽管道的热损失量超标率为42.9%。当前国内炼化企业蒸汽管道的保温技术水平与国外相比差距较大,国外保温管道选材时保温层厚度计算方法详细具体、内容丰富,保温管道结构新、导热率小、F水性好、寿命长。国内炼化企业的主要问题有以下几个方面:
(1)材料方面。水平管道上的软质保温隔热材料在服役期普遍存在保温层下沉现象,如图1-2所示,导致D端保温层减薄,保温系数显著降低,导致热损加速;硬质保温的接缝不能严格密封而形成“热通道”导致热损,同种保温隔热材料性能良莠不齐。
(2)设计方面。保温管道选材时保温层厚度计算方法参数取值范围模糊,不易操作;对于南北地域不同企业,有时不能因地制宜地选择保温隔热材料;保温结构设计不合理,下雨浸水后热量损失大,温降大,不JJ热损大,甚至直接影响生产。
(3)施工方面。各家施工单位的施工水平参差不齐,现场调研测得实际厚度与设计要求厚度存在差距,实际厚度小于设计厚度的管道数占整体管道样本数量20.4%。表1-5是管径为中325mm,介质温度为400℃条件下各家企业的保温层设计厚度。施工环节不规范,特别是保温损坏后的修补,不易达到原施工质量水平,引起保护层开裂、变形,导致保温性能降低,热量损失严重。
(4)日常运营维护不够重视。存在随意踩踏保温管道的现象,要注意保温结构的保护,若因操作需要不可避免的踩踏保温管道时,应在此部位搭设操作平台或保护装置。发现保温结构损坏,应及时修X复,X复标准应达到原设计要求。
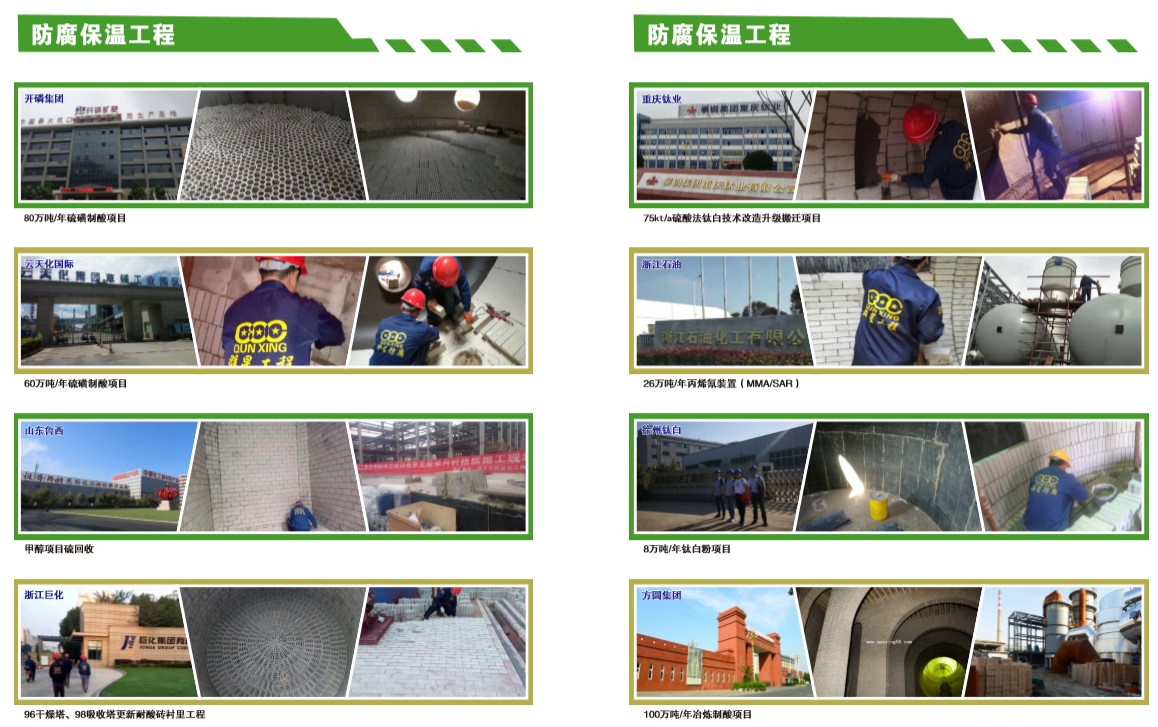